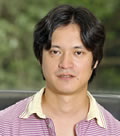
Developing a method of crystal growing organic molecules without impacting the environment, using ‘natural power’
Takeo MINARI RIKEN Special Postdoctoral Researcher
Next-generation electron devices using organic semiconductors, which are thin, light and flexible, are attracting attention as a new small-circuit technology for display, lighting and IC tags in a distribution system. Takeo Minari, a special postdoctoral researcher at RIKEN, was involved in research on the efficient production of one type of these electron devices, FET or field-effect transistors (as of April 2009 he is a MANA researcher at the National Institute for Materials Science, International Center for Nanoarchitectonics).
By using a cheap and eco-friendly printing method known as the selective surface application method, it was found that the environmental impact could be significantly reduced in addition to lowering capital investment and running costs.
Growing high quality organic semiconductor crystals on substrates
The use of organic semiconductors is expanding into many areas such as for cell phone displays. A semiconductor is a substance which is intermediate between a conductor, a material which lets electricity pass, such as metal, and an insulator, a material which does not let electricity pass. Conventional semiconductors for electronic devices are mainly made of inorganic substances such as silicon, but recently organic semiconductors such as those containing carbon, are becoming popular. The reasons are the possibilities for reduced costs, which have been difficult to achieve for organic semiconductors in the past, the viability of eco-friendly production processes, and other characteristics such as material flexibility.
However, there were hurdles to overcome when it came to establishing a production process for organic semiconductor devices. Minari explains,
‘Generally speaking, the circuit of an organic semiconductor device is prepared by depositing a thin polycrystalline film of the required material onto a substrate. The response and stability of the circuit when voltage is applied are heavily dependent on the quality of the crystals. For example, for the vapor-deposition technique, in which the required material for crystals is vaporized and deposited on a substrate, careful consideration needs to be given to the depositing conditions, and the formation of the crystal layers requires delicate control. The technique also requires a large-scale facility, since the deposition process is conducted in a vacuum. There are other issues, such as the lack of an established method of ensuring stable growth of the crystals to lower the defect rate, and mass production using this technique seems far away.
There are other techniques, generally known as solvent-based coating techniques, in which a material is dissolved in a solvent, applied on a substrate, and then crystallized as the solvent evaporates. These include spin-coating, in which a solvent is applied on a rotating substrate and a film is formed by centrifugal force, drop casting, in which a solvent is dropped onto a substrate and dried as is, and inkjet printing, in which a solvent is applied as tiny droplets as in a inkjet printer. However, all of these have shortcomings such as difficulties in controlling the growth of crystals as well as low throughput’.
A selective surface application method utilizing natural phenomenon
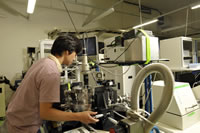
Organic crystal growth with the selective surface application method
On the other hand, the selective surface application method developed by the Minari team in collaboration with Dai Nippon Printing Co., Ltd. is by comparison very simple.
In the selective surface application method, organic semiconductor crystal growth is encouraged only in selective regions by patterning the wettability of the substrate surface. First, the whole of a substrate such as plastic is coated with a monolayer that is solvent-repellent. Then vacuum ultraviolet rays (VUV) are irradiated onto the areas where the organic crystals which will form the electronic device are required to grow. The areas where crystals are not required are covered with a metal mask so that they will not be exposed to the VUV. In this way, the areas of the solvent-repelling monolayer which have been irradiated by VUV are erased. The substrate is then subjected to surface-modified solvent affinity molecules, which trigger the formation of a monolayer with other characteristics in the areas where the previous monolayer was eradicated by VUV. The functional pattern of surface molecules formed in this way is called a molecular template.
‘When you apply a solution containing the organic semiconductor material onto a molecular template, the solution naturally moves to the areas without the solution-repelling monolayer, guided by the difference in the functionalities of the surface pattern. It then evaporates and starts forming crystals. The selective surface application method exploits this tendency of organic molecules to self-assemble’, Minari explains.
Minari goes into greater detail about the self-assembly process of organic molecules, an interesting phenomenon he is keen to exploit.
‘Organic molecules demonstrate various characteristics depending on their molecular skeletons and electronic states. This is why there is interaction of repulsion and affinity between the molecules and the solvents with repelling and non-repelling functionality. The selective surface application method uses this as the driving force to grow semiconductor crystals on target regions. Since it is a technique in accordance with natural law, it consumes less energy’.
The method demonstrates its full advantage especially in complicated circuits that require accuracy of under a few μm. The method is also beneficial for applications where simple but multiple circuits are laid out such as displays, solar panels and lighting, as well as complicated integrated circuits, which did not respond well to traditional coating techniques.
Reducing processing cost by using raw materials more efficiently
The selective surface application method is a bottom-up technique in which the molecules are collected in the required regions through their own interaction for the spontaneous formation of a device. Traditional techniques, on the other hand, were top-down techniques in which a circuit is made by first forming a multilayer of semiconductors and then erasing the unnecessary areas by such means as lithography. Minari’s method has proven successful in the following three areas where traditional methods have failed.
1. Large area, high throughput device fabrication
This is a process in which a large number of electronic devices are fabricated at once and is most suitable for mass production. For example, if the base material is flexible, the substrate can be rolled to be machine-fed and applied with solvent. When the elements have crystallized, it can finally be rolled onto another roller, checked and sent to the next production stage. The fabrication of devices using the same technique as printing is not such a remote dream.
2. Effective use of organic semiconductor materials
Growing crystals only in the required areas, eliminates the process of erasing unnecessary areas, resulting in the efficient use of organic semiconductor solvents and ultimately the conservation of precious resources. This also lessens the impact on the environment by reducing the kind of waste produced by the traditional methods.
Various materials can be used as a substrate, as long as they can take the abovementioned molecular template treatment. By using a plastic or polymer insulation layer as a base, next-generation electronics devices can be thin, light or bendable. Possible applications include a touch sensitive electronic catalog and menu order panel.
3. Reduction of equipment and facility costs
With this method, film patterns can be fabricated in a simple facility equipped with UV radiation. This is in contrast to the traditional methods that required large-scale facilities with vacuum deposition or inkjet equipment. The selective surface application method requires only UV radiation and solvent application equipment, thereby reducing energy consumption and making it an environmentally friendly technology. Minari concludes,
‘There are still many hurdles to overcome with regard to improving the quality of the device and we are trying out many ideas to do this. We are increasingly confident that we can put together electronic devices using the self-assembly characteristic of interacting molecules, and develop molecular electronics with low energy consumption’.
The research has already reached the stage where all components, including electrodes and wiring in addition to semiconductor layers, can be self-assembled using the selective surface application method. It will not be long before products made with this technology are on the market.